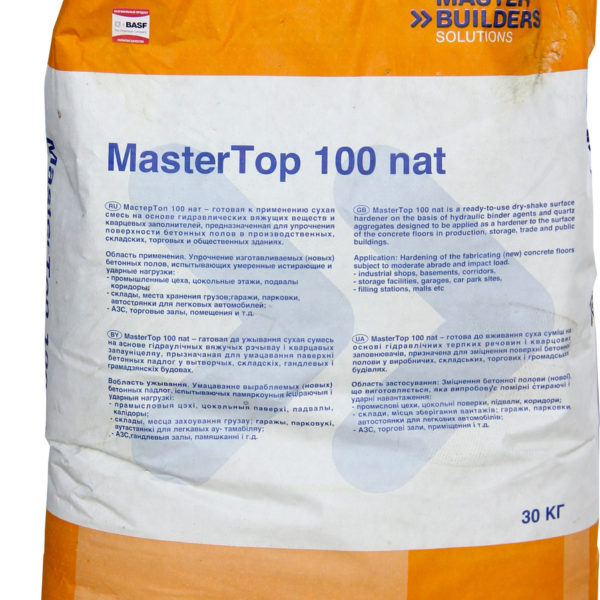
MASTERTOP 100 | Dry shake hardener for industrial floors | Dry shake toppings
Dry, quartz hardener for fresh concrete floors
Topping - shake hardener of industrial floors
Industrial floors for a warehouse
Industrial flooring for shop
Industrial garage flooring
COMPLETE SUPPLY
complete project package
HIGH QUALITY
goods from the world's leading manufacturers
Dry shake toppings
Master Top 100 | Dry mix, based on quartz and other mineral aggregates, for hardening the surface of freshly laid (new), industrial concrete floors.
-
MasterTop 100, dry mix for hardening the surface of new concrete floors;
-
Made on the basis of mineral aggregates and corundum;
-
It is applied as a dry powder on freshly laid concrete, when installing industrial floors.
-
Designed for rooms with medium and heavy industrial loads;
- Complies with EN 13813.
MasterTop - industrial floors for a warehouse
Cement shake hardener applications Mastertop 100 | Dry shake toppings
-
Wear-resistant coating designed to protect the surface of concrete floors subject to medium and high industrial loads.
-
Significantly reduces the formation of dust and increases the strength, wear resistance, durability of the concrete floor surface, in industrial warehouse floors.
- Industrial floors for garages.
-
Industrial floors for energy industry enterprises.
-
Industrial floors for car service.
-
Industrial floors for parking.
-
Industrial floors for loading bays.
-
Industrial floors for industrial complexes.
-
Industrial floors for shipyards.
-
Industrial floors for aircraft hangars.
-
Industrial floors for car wash.
- Industrial floors for heliports.
Mastertop - industrial floors with topping
Features and Benefits
-
A simple system for laying topped industrial floors.
-
The topping is applied to the fresh concrete surface.
-
When setting, the polymer components contribute to the absorption of moisture from the concrete by the hardener.
-
A durable wear-resistant coating is formed on the concrete surface.
-
Does not oxidize.
-
Increases the abrasion resistance of industrial concrete floors by 2-4 times.
- Topping, contains high-strength, quartz corundum filler.
-
Shake hardener for industrial floor, resistant to freeze-thaw cycles.
- Industrial floor with Mastertop 100 topping, resistant to salt anti-ice powders.
MasterTop - industrial floors for the military industry
Specifications
Material composition |
Contains mineral fillers and special cement modified with polymers
|
Color |
natural, grey, red, green
|
Compressive strength |
≥С30 (30-60 N/mm2)
|
Flexural strength TS EN 196 (28 in.) |
F5 (5-15 N/mm2)
|
Abrasion resistance |
A9 (0-9cm3/50cm3)
|
Application procedure
-
The structure of the concrete slab on which the hardener is planned to be laid must be designed in such a way as to withstand all loads planned in the room;
-
The hardener improves the properties of the concrete surface, such as resistance to abrasive wear, impact resistance, reduces dusting;
-
But the hardener does not affect the strength characteristics of the concrete slab under it, its compressive strength, bending, rupture;
-
Cracks formed in the concrete base due to unsuitable slab construction, laying errors, excessive operating loads will also appear on the surface of the hardener;
Surface hardener MasterTop 100 must be applied under the conditions specified below:
-
on concrete or screed, right on the ground;
-
on the carrier plate;
-
on a floating screed;
- on a tied screed.
Surface preparation before laying the screed
-
If it is planned to apply a surface hardener to a screed poured over existing concrete, the appropriate type of screed should be selected (floating or bonded);
-
The surface must be processed by various methods to obtain a rough texture, where necessary;
-
The existing concrete surface must be saturated with water at least one day before the screed is laid;
-
Remove excess water from the surface;
-
Before laying the screed, install the formwork along the edges of the card;
-
Heat shrink seamsmust be made according to the requirements of the project;
-
The poured screed must be separated from walls and columns, for example, using sheets of extruded polystyrene, 1 cm thick, which will allow the screed to work without restrictions, expand, without cracking;
-
After laying the screed, the joints can be filled using sealants MasterSeal CR125, MasterSeal CR170/170, MasterSeal NP474;
-
To obtain smooth, beautiful edges of the concrete slab / screed, the formwork should be thoroughly cleaned and formwork lubricant, MasterFinish should be applied;
-
The formwork must have the same height as the height of the planned screed/concrete slab;
-
Formwork with a "tongue" and a groove prevents the effect of subsidence of concrete slabs at cold joints under heavy loads;
-
The use of tie rods between the plates prevents the plates from moving longitudinally, and thus the plates do not create excessive shear pressure on the sealant, which increases its service life.
Spacers or fixtures for fittings
-
Steel reinforcement, which will be used in the project, must be installed on supports, racks-retainers for reinforcement from below;
-
When the reinforcement is installed on the floor without the use of supports, the reinforcement will be in the intermediate layer between the slabs and will not have any adhesion to the concrete screed, will not restrain movement, stress and deflection, which, as a result, will lead to failure under heavy load;
- If single layer reinforcement is used, then the reinforcing mesh should be installed in the middle of the depth of the concrete slab.
Topping - shake hardener for concrete floors
Reinforcement of a concrete slab
-
Steel reinforcement should not protrude beyond the concrete surface;
-
If a steel mesh is installed, it must be overlapped one on top of the other;
-
Shrinkage and cold joints must be formed in such a way as to control any change in the shape or movement of the concrete without cracking;
-
In order to control the movements in these joints so that they occur only in the horizontal plane, in the right direction, the reinforcement must protrude from the slab, and enter into the adjacent slab;
-
The branch entering the adjacent slab must be in a plastic case to ensure the mobility of the armature branch;
-
Only after putting on the cover should the adjacent slab be poured;
-
This will prevent vertical and longitudinal movement of cold joints during the movement of the plates.
Cutting seams in concrete floors
Primer application
-
In a monolithic bonded slab, it is required to provide adhesion between the old and new concrete, before laying a layer of new concrete, using MasterBrace ADH 1420 epoxy adhesive or MasterCast 125 polymer cement concrete with adhesion improver.
-
In floating screeds, it is mandatory to use a concrete separating the layers, a sheet of polyethylene membrane that prevents adhesion between the layers of old and new concrete.
Install of industrial floors
Pouring concrete for industrial floors with Mastertop 100 topping
-
A concrete slab must be poured in a structure that clearly corresponds to the project;
-
Before pouring concrete, the required number of bags of MasterTop 100 hardener should be prepared, in accordance with the recommended consumption rates;
-
The thickness of the slab/screed for applying MasterTop 100 must be at least 70mm;
-
The water-cement ratio should be at least 0.45 and the concrete class should be at least C25;
-
During the pouring process, a vibrator should be used in the formwork to compact the concrete structure;
-
Before the release of water begins, it should be smoothed out with a trowel and a wooden rule;
-
The released water should be removed from the surface with a long wooden tool;
Installation of topping floors
Application of Mastertop 100 topping for industrial floors | Dry shake toppings
-
The required number of bags of MasterTop 100 hardener should be prepared in advance, in accordance with the recommended consumption rates;
-
Application should be made in accordance with the recommendations below;
-
Before applying the powder of the material, it is necessary to remove with a spatula a triangular section of concrete along the edges of the slab at the joints measuring approximately 50 * 50 mm, and fill the cavity with a mixture of MasterTop 100 and a very small amount of water;
-
This will ensure the strength of the edge of the slab at the seams under high loads;
-
The hardener should not be applied in a chaotic manner to different parts of the slab, this can cause delamination of the coating;
-
The distribution of the hardener should be started when the concrete has gained such strength, when the foot in the shoe of a person standing on the surface falls only 5-15mm into the concrete;
-
The hardener should not be applied in places, but only as evenly as possible distributing it over the surface and leveled by the rule;
-
Usually, the topping is spread over the surface, using dedicated dosing carts.
Wear resistant topping floors
-
If the hardener is applied in places, it should be distributed over the surface, removing excess;
-
In the first application, about 2/3 of the required amount of powder should be added;
-
The powder must absorb moisture from the concrete slab from below, while changing color;
-
Immediately after the color change, the hardeners carry out the first grouting with a concrete finishing machine with a disc;
-
Grouting should begin near walls, columns, openings in these places, moisture loss occurs most quickly);
-
It is necessary to rub the topping until a uniform surface consistency is obtained;
-
In hard-to-reach places, grout with a hand tool;
-
Immediately after grouting the first portion of the hardener, the rest of the hardener powder should be added so that it has time to soak with moisture from the base, and repeat the previously listed operations;
-
After troweling with a disc, troweling with blades should be done until a shine appears on the surface;
-
After laying, it is mandatory to apply membrane-forming impregnations (MasterKure, MasterTop C) to protect the surface from dehydration, which leads to the formation of shrinkage cracks, cobwebs, dust formation during operation;
-
With it, the maximum quality of the MasterTop 100 floor is achieved;
-
Care should be provided both in summer and winter;
-
To select a membrane former, please contact your local BASF representative, FLOORTOP;
- To avoid the formation of chaotic shrinkage cracks, cutting joints as soon as possible, immediately after the concrete has gained initial strength, when the edge of the joint does not break off during cutting.
-
At a temperature of +18 +20ºС, this is usually 1-2 days;
-
Joints must be filled with appropriate sealants MasterSeal CR125, MasterSeal CR170/170, MasterSeal NP474.
Industrial floors for the military industry
Consumption Mastertop 100
-
4-8 kg/m2 of powdered product/ per 1 m2 of surface;
- Colored hardener should be applied at a rate of at least 7kg/m2.
Precautionary measures
-
During laying, the ambient temperature should be in the range from +5 ºС to +35 ºС;
-
The product must be applied by qualified installers;
-
The hardener improves the properties of the concrete surface, such as resistance to abrasive wear, impact resistance, reduces dusting;
-
The hardener does not affect the strength characteristics of the concrete slab under it, its compressive strength, bending, rupture;
- Cracks formed in the concrete base due to unsuitable slab construction, laying errors, excessive operating loads will also appear on the surface of the hardener.
-
The thickness of the slab/screed for applying MasterTop 100 must be at least 70mm;
-
The water-cement ratio must be at least 0.45 and the concrete class must be at least C25;
-
The terms of work and hardening of systems based on cement depend on the temperature of the environment and the surface, the relative humidity of the air;
-
At low temperatures, hydration slows down, which prolongs the working time with the mixture and the setting time;
-
High temperatures accelerate hydration, resulting in reduced working time with the mixture and setting time;
-
For complete curing of the material, the ambient and surface temperatures must not fall below the specified minimum limits.
Cleaning tools
-
After use, used tools and equipment should be washed with water;
-
MasterTop 100 after hardening, can be cleaned from the surface, only mechanically;
Package
25 kg polyethylene reinforced kraft paper bag.
Storage
-
The material must be stored in its original packaging in a cool, dry place (at +5°C +25°C;
-
Short-term storage allows arrangement of up to 3 pallets one by one;
-
Long-term storage of pallets - only in one row.
Best before date
Under appropriate storage conditions - 12 months from the date of manufacture;