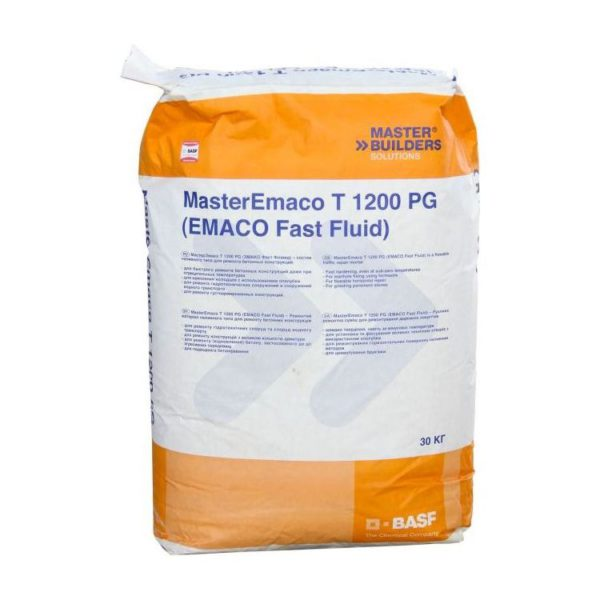
MasterEmaco T 1200 PG | Concrete repair in winter
Cement based, fast curing mortar for repairing concrete floors and roads
Repair at negative ambient temperatures
Concrete repair on the street
Repair of concrete roads
Concrete site repair
Warehouse concrete floor repair
COMPLETE SUPPLY
complete project package
HIGH QUALITY
goods from the world's leading manufacturers
MasterEmaco T 1200 PG | Ready-to-use material, in the form of dry concrete mix.
-
MasterEmacoT 1200 PG | non-shrinking, fast-hardening dry mix of bulk type , containing polymer fibers, intended for structural repair of concrete and reinforced concrete, in a short time. Can be used at temperatures down to -10°C.
-
MasterEmaco T 1200 PG - when mixing the dry mixture of Emaco with water, a non-shrinking, non-separating repair compound is formed, which has high adhesion to steel and concrete, even in an aggressive environment.
-
Thanks to its properties, MasterEmaco T 1200 PG allows for the restoration of concrete and reinforced concrete structures by casting to a thickness of 10 to 150 mm , when the most important requirement is the speed of curing (including at low temperatures).
- Complies with EM 1504-3^4.
Areas of application for Emaco repair mortar
-
Repairing cracks in a concrete floor in a warehouse.
-
Warehouse concrete floor repair.
-
Fast concrete repair.
-
When repairing concrete pavements of roads, airfields, parking areas and bridges.
-
Also, Emako dry mix is used to repair hydraulic structures and water transport structures.
-
For underwater concreting, as well as for repair work, in a variable water level.
-
For the repair of reinforced (including prestressed) structures - beams, supports, bridge slabs, etc.
-
For the repair of heavily reinforced surfaces where manual and machine application is not possible.
-
For monolithic joints of prefabricated reinforced concrete structures (concrete supports, slabs, etc.).
-
For quick repair (restoration) of concrete exposed to aggressive environments containing chloride and sulfate ions, including for protection against sea water.
Properties and benefits of Emako concrete repair mortar
-
Repair composition Emako, has an extremely fast set of strength;
-
The object to be repaired, with Emaco mixture , can be put into operation in 2 hours;
-
Repair mortar Emako has very high early and final strength;
-
Master Emako is very easy to use;
-
With the introduction of an additional amount of crushed stone into the dry repair mix Emako , it is possible to increase the thickness of the application of the composition, obtaining microconcrete.
-
After mixing with water, Emako dry mix is easy to spread on a horizontal concrete base.
-
The flowing and mobile consistency of the Emako repair compound allows you to quickly repair local areas.
-
Emako concrete , can be used at low temperatures, down to -10 ° C;
-
MASTER EMACO , has high adhesion to the concrete base and durability;
-
The risk of cracking is minimized by controlled expansion and the use of PAN fibers;
-
EMACO horizontal concrete repair mix , resistant to freeze/thaw cycles;
- After the curing of the Emako concrete mixture , the repaired concrete base creates good protection for the reinforcement due to low water permeability and resistance to carbonation.
Specifications
Compound |
Contains mineral fillers and special cement modified with polymers
|
Color |
Grey
|
Aggregate size |
2.5 mm
|
Chloride content |
|
Layer thickness min-max |
10-100mm (repair)
25-150mm (gravy) |
Density of fresh mortar |
2250 kg/m3
|
Water dosage |
2.7-3.2 l
|
Removal of damaged concrete
-
The edges of the defective area should be contoured with a diamond tool, perpendicular to the repaired surface, to a depth of at least 10 mm;
-
Degraded concrete must be removed using a light hammer drill, needle gun or sandblaster;
-
The base surface must have a roughness of at least 5 mm before applying the Emaco repair mortar;
-
This operation is important to ensure good adhesion of MasterEmaco T 1200 PG to the repaired surface.
Rebar cleaning
-
It is necessary to clean the fittings from rust;
-
If the repaired structure is operated in environments aggressive to concrete and steel, it is recommended to treat the reinforcement with MasterEmaco P 300 material (at positive temperatures).
-
Attention: at negative temperatures MasterEmaco P 30 0 cannot be used.
Impregnation of the substrate with water before applying the EMACO self-leveling repair mortar
(carrying out works at a temperature of 0°C and above)
-
Before laying MasterEmaco T 1200 PG, thoroughly impregnate the surface to be repaired with water;
-
Excess water should be removed with compressed air or rags;
-
The surface before pouring MasterEmaco T 1200 PG must be damp, but not wet.
-
When working at low temperatures, the base is not moistened.
-
For better adhesion of the repair material to the surface, it is recommended to apply an adhesive composition (a thin layer of MasterEmaco T 1200 RG );
-
To remove snow, ice and warm the base, it is necessary to process the repaired area with a burner;
-
Warming up the base (carrying out work at temperatures from 0°С to -10°С);
-
Before laying the mixture, MasterEmaco T 1200 PG, the surface to be repaired must be warmed up to a positive temperature;
-
Warming up is carried out with thermomats, infrared emitters or blowtorches;
-
This operation is necessary to remove possible frost from the prepared base and prevent heat loss during the hydration reaction of the repair composition.
formwork
-
The formwork must be made of strong material, be airtight and securely fastened in order to contain the pressure of the repair compound after pouring;
-
The formwork must have a special air outlet located at the top if it is a vertical structural member (such as the side of a support) or only on one side if it is a horizontal structural member (beam bottom surface).
-
Before pouring, the formwork must be saturated with water so that it does not take water from the repair composition, dehydrating it;
-
It is necessary to seal the formwork to prevent leakage of the repair compound;
-
To do this, you can use MasterEmaco T 1200 PG material itself with a thick consistency or other suitable materials, for example, MasterSeal 590;
-
Do not seal the formwork with various fabric-based materials, as they may be difficult to remove;
- At negative ambient temperatures, it is necessary to cover the formwork with heat-insulating material from the outside to prevent heat loss.
Preparation of dry mix Emako
Before mixing MasterEmaco T 1200 PG with water:
-
make sure that all the necessary materials (mixer, carts, buckets, trowels, etc.) are at hand;
-
check that the amount of material available will be sufficient;
-
check the implementation of the preliminary work prescribed in the section " Instructions for repair work";
- Mix only as much Emako repair compound as you can use within 15 minutes.
For the correct preparation of the repair composition, follow the instructions below:
-
open the bags with MasterEmaco T 1200 PG dry mix necessary for work, shortly before mixing;
-
add water at the rate of 2.7-3.2 liters of water per 25 kg MasterEmaco T 1200 PG bag ;
-
at an ambient temperature above +30°C, it is necessary to use cold water for mixing;
-
this will extend the pot life of the concrete mix;
-
at an ambient temperature below +5°C, it is necessary to use hot water for mixing (from +30 to +45°C);
-
dry repair mixture during mixing, must have a temperature not lower than +5°C. This will speed up the exothermic reaction;
-
turn on the mixer, quickly and continuously add MasterEmaco T 1200 PG;
-
after the entire MasterEmaco T 1200 PG dry mix is poured in, mixing should be continued for at least 3 minutes;
-
the ready-to-use mixture should be fluid, without lumps.
-
to knead a small amount of MasterEmaco T 1200 PG, you can use a low-speed drill (no more than 300-400 rpm) with a spiral nozzle;
-
Mixing by hand is not allowed;
-
If it is necessary to create a layer with a thickness of more than 100 mm, washed gravel (crushed stone) should be added in an amount of up to 30% by weight of the dry mixture;
-
If you have special requirements, you should seek advice from FLOORTOP specialists.
Laying
-
Prepared repair mortar MasterEmaco T 1200 PG should be poured continuously without vibration;
-
Filling must be carried out on one side to prevent air entrapment;
-
It is advisable to bayonet the laid mixture;
-
The surface of the material laid on a horizontal surface can be leveled with a float.
Maintenance of Emako repair mortar after laying
-
Repaired areas must be kept in conditions that exclude water evaporation for 24 hours;
-
To create such conditions, film-forming materials are used or the repaired surface is subjected to moisture care;
-
In the absence of the possibility of using water for wetting, acrylic membrane formers are used as sealing compositions.
-
At negative temperatures, the repaired area must be covered with heat-insulating material or rags to prevent heat loss during exothermy, as well as to avoid cracking.
Emaco repair mix consumption
2.00 kg/m2 powder product per 1 mm layer thickness.
Precautions for handling EMACO blends
-
Do not use at temperatures below -10°C or above +30°C;
-
Do not add foreign ingredients to the solution (cement, sand, additives);
-
For laying Emaco concrete mix with a thickness of more than 100 mm, add 7.5 kg of pure crushed stone of fraction 48 or 8-16, per 1 bag of 25 kg MasterEmaco T1200 PG;
-
Do not use a vibrator to level the composition;
-
Do not mix fresh Emako dry mix powder or water into the previously mixed mix;
-
Do not violate the dosage of water when mixing the dry mix Emako;
-
Protect from rain, freshly laid repair mortar Emako.
Cleaning tools
-
After use, used tools and equipment should be washed with water;
-
MasterEmaco T 1200 PG, after hardening, can only be cleaned mechanically from the surface.
Emako dry mix packaging
Kraft paper bag with polyethylene reinforcement, 25 kg.
Storage of Emako dry mix
The material must be stored in its original packaging in a cool, dry place (at a temperature of +5°C ... +25°C).
Shelf life of dry mix Emako
Under appropriate storage conditions - 12 months from the date of manufacture.